Laser Cleaning: A Safer, Smarter Way to Clean Surfaces
In industrial settings, surface cleaning is an essential part of maintenance, repair and preparation for coatings or welding. Traditional methods like sandblasting, chemical cleaning, and grinding can be messy, time-consuming and potentially hazardous. Enter laser cleaning. A revolutionary, non-contact technology that is transforming the way industries approach surface preparation.
At Rapid Welding, we recognise the importance of using safe, efficient and cost-effective solutions for surface cleaning. Here’s our expert guide to help you choose with confidence. We’ll take a look at the benefits of laser cleaning, how it works and what to look for when picking the right laser cleaning system for your needs.
But first…
What Exactly Is Laser Cleaning?
Laser cleaning is an advanced, non-abrasive technique that uses high-intensity laser beams to remove rust, paint, oil, oxides and other contaminants from surfaces. The process works by directing a focused laser onto a material, which absorbs the laser energy, causing the unwanted layer to vaporise or be ejected through thermal expansion. This leaves the base material intact, making it an excellent choice for delicate or high-value components.
Unlike mechanical or chemical cleaning methods, laser cleaning offers a precise, eco-friendly, and low-maintenance solution for surface preparation. Comparison below.
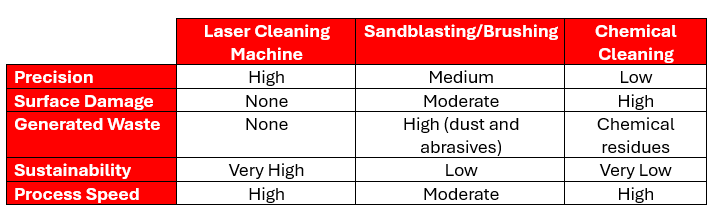
The laser cleaning market is expected to grow from £520 million in 2023 to £910 million by 2032 (Straits Research), showing that more people are choosing cleaner and safer ways to remove rust and dirt.
Why Choose Laser Cleaning?
Well, there are a lot of reasons:
1. Safe and Environmentally Friendly
Laser cleaning eliminates the need for harsh chemicals, abrasives and excessive waste. Since it operates without consumables like blasting media or chemical solvents, it significantly reduces health risks for anyone who uses it and minimises environmental impact.
2. Non-Damaging to the Base Material
Traditional cleaning methods can cause pitting, warping or other damage to sensitive surfaces. Laser cleaning; however, selectively removes contaminants without affecting the integrity of the underlying material, making it ideal for use on metals, composites and even historical artifacts.
3. High Precision and Efficiency
Laser cleaning provides pinpoint accuracy, allowing operators to remove coatings or rust from specific areas without affecting surrounding surfaces. The process is fast, automated and highly efficient, significantly reducing downtime compared to manual cleaning methods.
4. Reduced Maintenance and Consumable Costs
Since laser cleaning doesn’t rely on consumable materials like sand or chemicals, it offers long-term cost savings. Additionally, laser systems have fewer moving parts, meaning less maintenance and a longer lifespan compared to traditional blasting equipment.
5. Versatile Applications
Laser cleaning is becoming widely used across multiple industries, including:
- Welding and Fabrication – Pre-weld preparation and post-weld oxide removal.
- Aerospace and Automotive –Paint stripping, rust removal and degreasing.
- Marine, Oil and Gas – Corrosion removal on metal surfaces.
- Electronics and Precision Engineering –Cleaning delicate components without surface damage.
- Cultural Heritage Restoration – Safely restoring stone, wood and metal artifacts.
Choosing the Right Laser Cleaning System
Not all laser cleaning systems are the same, so selecting the right one for your needs is crucial. Here are some key factors to consider:
1. Laser Power
The power of a laser cleaning system determines its speed and effectiveness. Low-power lasers (20W-100W) are suitable for delicate cleaning, while high-power lasers (200W-2000W) offer rapid removal of rust, paint and industrial contaminants.
2. Portability and Automation
Some laser cleaning systems are designed for handheld operation, offering flexibility for onsite work, while others are fully automated for high-volume industrial applications.
3. Pulse vs. Continuous Wave Technology
Pulsed lasers offer greater precision and are ideal for removing thin layers of contamination.
Continuous wave lasers provide higher power and are more effective for large-scale industrial cleaning tasks.
4. Safety Features
Laser cleaning systems should come with built-in safety mechanisms, such as fume extraction, interlocks and protective enclosures to ensure safe operation.
Laser Cleaning Machines at Rapid Welding
To meet the diverse needs of our customers, Rapid Welding offers a range of advanced laser cleaning machines. To help you out, here are some of our best laser cleaning equipment:
1. LC Lasers LC-Clean P 300W Laser Cleaning Machine
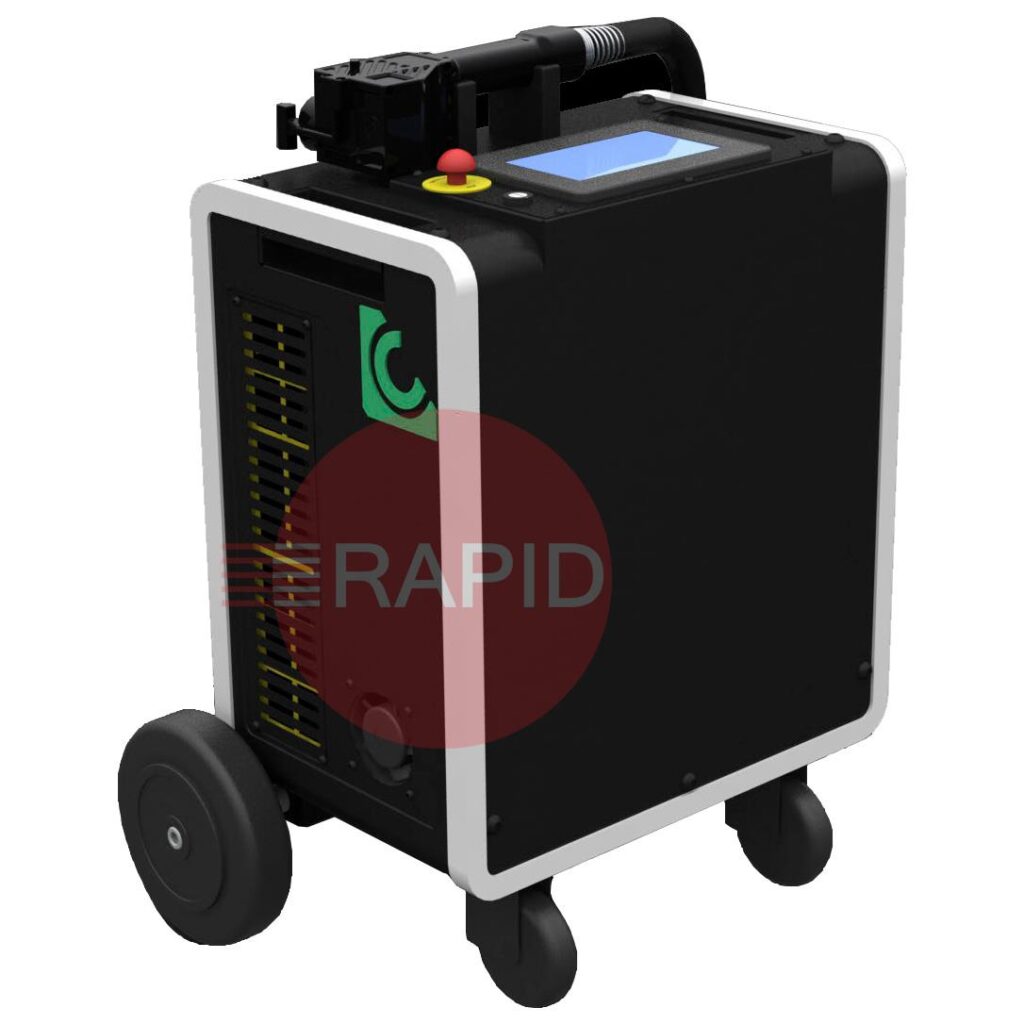
- Power: 300 Watts
- Features:
- Integrated control system for adjusting speed, laser output shape and beam width.
- Non-contact cleaning that preserves the base material.
- Environmentally friendly operation without the need for chemicals or abrasives.
- Applications: Ideal for removing rust, paint, grease, oils and various contaminants from metal surfaces.
2. LC Lasers LC-Clean P 500W Laser Cleaning Machine
- Power: 500 Watts
- Features:
- Enhanced power for faster and deeper cleaning applications.
- User-friendly interface with customisable settings to suit various tasks.
- Minimal maintenance requirements due to robust design.
- Applications: Suitable for heavy-duty industrial cleaning, including thick rust and paint removal, as well as surface preparation for welding and coating.
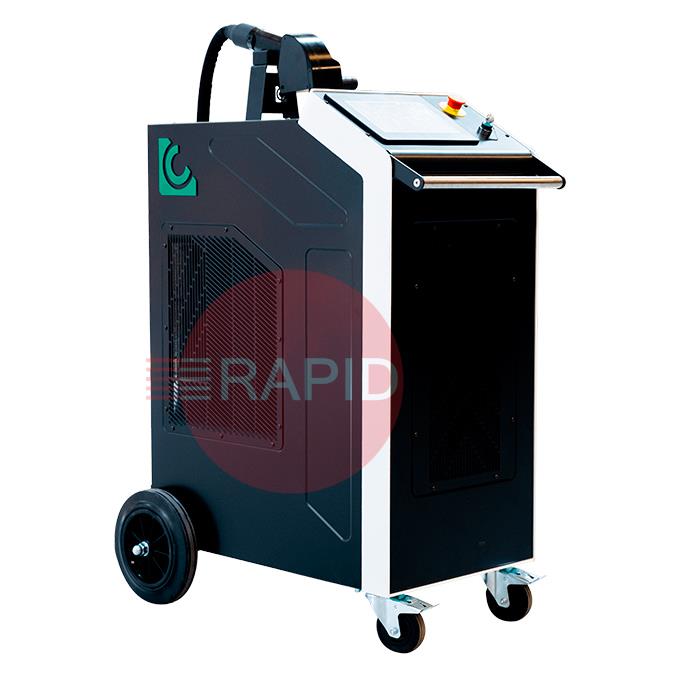
Both machines are designed with versatility and efficiency in mind, ensuring that you can achieve the best cleaning results, while maintaining the integrity of your components.
So, Is Laser Cleaning Right for You?
If you’re looking for a safer, cleaner and more efficient alternative to traditional surface cleaning methods, laser cleaning could be your perfect solution. Whether you need precision cleaning for delicate components or heavy-duty rust removal, this technology offers an unmatched combination of performance and sustainability.
At Rapid Welding, we stay ahead of the latest welding and surface cleaning technologies. You are always welcome to contact our friendly team of laser experts to learn more about how laser cleaning can improve your work.
Learn More About a Safer, Smarter Way to Clean Surfaces with Rapid Welding
Interested in upgrading your cleaning process? Browse our selection of laser systems and accessories here:
Come and see laser cleaning in action! Sign up for a demo and see for yourself how it can make your job quicker and easier.
Contact us today for expert guidance on finding the right system for your needs. Call us on +44 (0) 23 92 214 214, email webenquiries@rapidwelding.com or visit rapidwelding.com.