In the dynamic world of manufacturing and construction, the importance of welding remains steadfast. Welding, an age-old craft, has consistently evolved to meet the needs of diverse industries, from automotive to aerospace. As we hope you know by now, the Rapid Welding team are committed to keeping our clients at the forefront of welding technology, and we're excited to share a glimpse of what we think the future holds for the sector. Here are some of the most promising innovations on the horizon.
- Augmented Reality (AR) and Virtual Reality (VR) in Training: Welding requires precision and skill. Traditionally, acquiring these skills required extensive hands-on training. However, with the advent of AR and VR technology, trainees can now immerse themselves in a simulated welding environment, honing their skills without wasting materials or risking injuries.
- Automation and Robotics: While automated welding isn't new, the sophistication and accessibility of these solutions are continuously advancing. Robotic welding arms, guided by advanced sensors and AI, can execute intricate welds with unmatched consistency and speed. For businesses, this means reduced costs, faster production rates, and enhanced product quality.
- Advanced Welding Techniques: New welding methods are emerging to cater to the unique requirements of modern materials and applications. Techniques like Cold Metal Transfer (CMT) welding allow for reduced heat input, making it suitable for materials that are sensitive to high temperatures.
- The Advancement of Laser Welding: Laser welding stands out for its precision, versatility, and speed. Ideal for joining tiny components, it's becoming crucial in industries like electronics and aerospace. With its reduced heat-affected zone, the risk of material distortion is minimised. As the technology becomes more integrated with real-time monitoring systems, its role in modern manufacturing is set to expand significantly.
- Green Welding: As industries across the board grapple with environmental concerns, welding is no exception. The push for eco-friendly welding methods is leading to the development of processes that reduce energy consumption, minimise harmful emissions, and utilise sustainable materials.
- Enhanced Quality Control with AI: Quality assurance is paramount in welding. With the integration of AI-powered inspection systems, businesses can now instantly detect and rectify welding defects, ensuring that every weld meets the highest standards of quality.
- 3D Printing and Welding: 3D printing, or additive manufacturing, and welding are converging. Welders can now utilise specialized 3D printers that extrude metal, essentially "printing" welds layer by layer. This innovation is especially promising for creating complex, custom components with intricate welds.
Exciting times for the industry
We think the world of welding is on the brink of a technological renaissance. As the UK’s leading distributor of quality welding equipment, we're thrilled to be part of this journey, helping our clients navigate and harness these innovations for their success. The horizon is bright, and the future of welding promises greater efficiency, sustainability, and possibilities than ever before.
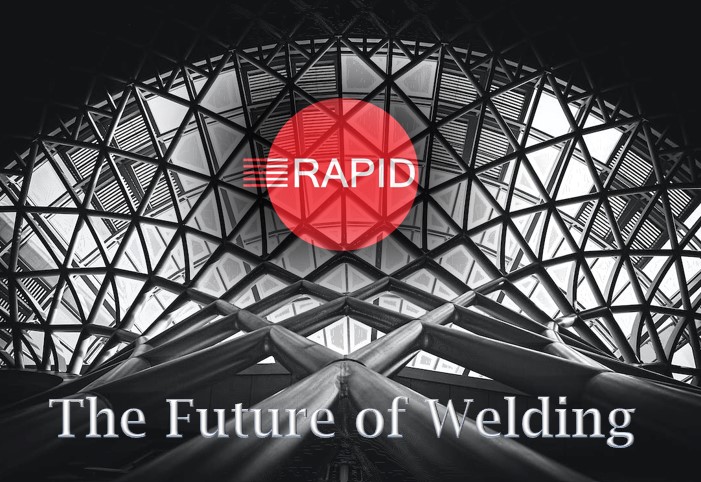
Leave a Comment